How to Choose the Right Saw for Cutting Flooring Materials
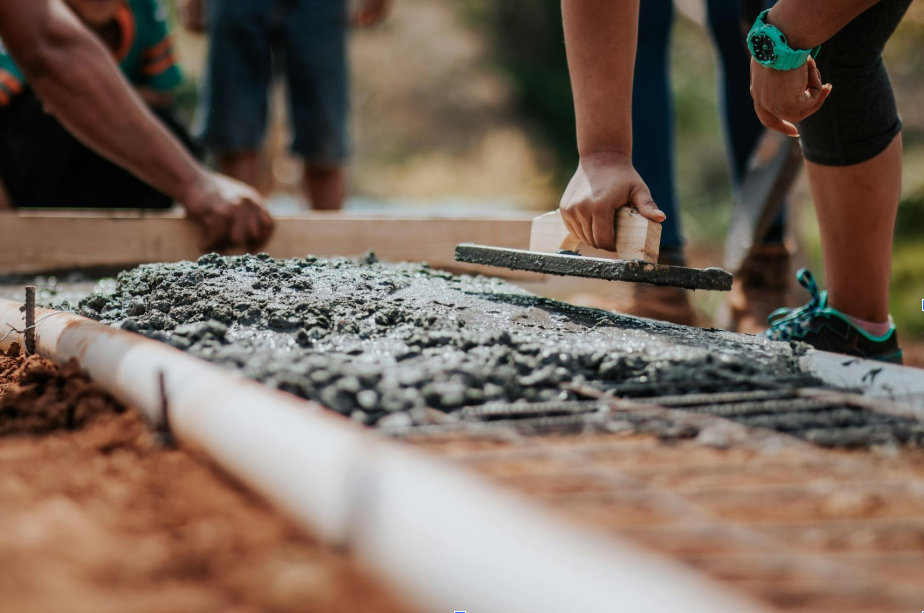
Introduction to Flooring Material Cutting
Selecting the appropriate saw for cutting flooring materials represents one of the most critical decisions in any flooring installation project. The quality of your cuts directly impacts the final appearance, fit, and longevity of your flooring installation. Whether you’re a professional contractor handling multiple projects or a homeowner embarking on a DIY flooring renovation, understanding the nuances of different saw types and their applications will save you time, money, and frustration.
The flooring industry has evolved dramatically over the past few decades, introducing innovative materials that require specialized cutting techniques and tools. From traditional hardwood planks to modern luxury vinyl tiles, each flooring material presents unique challenges that demand specific saw capabilities. The wrong tool choice can result in chipped edges, splintered surfaces, or imprecise cuts that compromise the entire installation.
Modern flooring installations demand precision that extends beyond basic functionality. Today’s homeowners and commercial property owners expect seamless transitions, tight joints, and professional-grade finishes. Achieving these standards requires not only skill and experience but also the right cutting tools that can handle the specific demands of each material type. The investment in quality saws pays dividends through improved efficiency, reduced waste, and superior final results.
Understanding Different Types of Flooring Materials
Hardwood flooring remains one of the most popular choices for residential and commercial applications, but it presents unique cutting challenges. Solid hardwood planks require clean, precise cuts that preserve the wood’s natural grain patterns while preventing splintering and tear-out. The density and hardness of different wood species affect cutting requirements, with exotic hardwoods like Brazilian cherry or teak demanding more aggressive cutting approaches than softer domestic woods like pine or poplar.
Engineered hardwood combines the beauty of natural wood with enhanced stability through its layered construction. These materials typically feature a hardwood veneer over a plywood or high-density fiberboard core. The multi-layer construction can cause delamination if cut improperly, requiring saws with fine-tooth blades and controlled cutting speeds. The thickness variations in engineered products also influence saw selection, as thicker planks may require more powerful tools.
Laminate flooring has revolutionized the industry by offering wood-like appearance at affordable prices. However, laminate’s synthetic composition creates unique cutting challenges. The high-density fiberboard core combined with the photographic wear layer can quickly dull standard wood-cutting blades. Laminate also tends to chip along cut edges, particularly when cutting across the grain direction, requiring specialized blade designs and cutting techniques.
Luxury vinyl planks and tiles have gained tremendous popularity due to their water resistance and realistic appearance. These materials cut differently than wood products, often requiring specialized vinyl-cutting blades or even score-and-snap techniques for straight cuts. The flexibility of vinyl materials can cause them to bend or move during cutting, necessitating proper support systems and cutting approaches.
Ceramic and porcelain tiles present entirely different cutting requirements, often necessitating wet saws or specialized tile cutting tools. The hardness and brittleness of ceramic materials require diamond-impregnated blades and water cooling systems to prevent overheating and cracking. Natural stone tiles add another layer of complexity, with variations in hardness and grain structure affecting cutting approaches.
See also: How to Choose the Right Saw for Cutting Flooring Materials
Essential Factors to Consider When Choosing a Saw
The specific requirements of your flooring project should drive your saw selection process. Project scope plays a crucial role in determining whether you need a portable saw for small repairs or a heavy-duty stationary saw for large installations. Consider the total square footage, the complexity of cuts required, and the timeline for completion when evaluating different saw options.
Blade compatibility represents another critical consideration that often gets overlooked. Different saw types accommodate specific blade sizes and mounting systems, limiting your options for specialized blades. Ensure your chosen saw can accept the blade types optimal for your flooring materials. Some saws offer tool-free blade changes that significantly improve efficiency during projects requiring multiple blade types.
Power requirements vary significantly between saw types and directly impact cutting performance. Corded saws typically provide consistent power delivery but require electrical access throughout the work area. Cordless saws offer superior mobility but may have limited runtime or reduced power compared to corded alternatives. Battery technology continues improving, with newer lithium-ion systems providing longer runtime and faster charging capabilities.
Cutting capacity encompasses both the maximum material thickness and the maximum cut length your saw can handle. Flooring materials range from thin vinyl tiles to thick hardwood planks, requiring saws with appropriate cutting capacities. Consider not only current project requirements but also potential future needs when evaluating cutting capacity specifications.
Accuracy and precision requirements depend on your skill level and project expectations. Professional installations demand tight tolerances and perfect cuts, while DIY projects may allow for slightly less precision. Some saws include built-in measuring systems, laser guides, or other accuracy-enhancing features that can improve cut quality and reduce waste.
Circular Saws for Flooring Applications
Circular saws represent the most versatile and commonly used tools for flooring installations. Their portability, power, and cutting capacity make them suitable for a wide range of flooring materials and applications. Modern circular saws feature improved blade guards, ergonomic designs, and enhanced safety features that make them safer and more user-friendly than previous generations.
The cutting depth adjustment capability of circular saws allows for precise control over cut depth, essential when working with different flooring thicknesses. This feature proves particularly valuable when cutting through subflooring materials or when making partial cuts for flooring transitions. Most quality circular saws offer easy-to-read depth adjustment scales that ensure consistent cutting depths across multiple cuts.
Bevel cutting capabilities extend the versatility of circular saws, allowing for angled cuts needed for flooring transitions, stair nosing, and decorative elements. The ability to adjust the saw base plate angle while maintaining cutting accuracy opens up numerous possibilities for complex flooring installations. Some advanced models include preset bevel stops at common angles, speeding up repetitive angled cuts.
Dust collection systems on modern circular saws help maintain clean work environments and improve cut visibility. Effective dust collection becomes particularly important when cutting materials that produce large amounts of sawdust or debris. Some saws include built-in dust ports that connect to shop vacuums, dramatically reducing cleanup time and improving air quality in enclosed spaces.
Blade selection for circular saws depends entirely on the flooring material being cut. Fine-tooth blades work well for laminate and engineered materials, while aggressive tooth patterns excel with solid hardwood. Specialty blades designed specifically for flooring applications often feature alternate top bevel tooth configurations that minimize tear-out and produce cleaner cuts.
Miter Saws and Their Flooring Benefits
Miter saws excel at making precise crosscuts and angle cuts, making them indispensable tools for flooring installations requiring accurate length cuts and complex angles. The fixed cutting position and integrated fence systems of miter saws ensure consistent, repeatable cuts that maintain the precision necessary for professional-quality flooring installations.
Compound miter saws add bevel cutting capabilities to the standard miter saw functions, allowing for simultaneous miter and bevel cuts. This capability proves invaluable when installing flooring around complex architectural features, creating custom transitions, or working with irregular room layouts. The ability to make compound cuts in a single operation saves time and improves accuracy compared to making separate cuts.
Sliding compound miter saws extend the cutting capacity by incorporating a sliding mechanism that allows the saw head to move forward and backward during the cut. This feature dramatically increases the crosscut capacity, enabling cuts across wider planks or multiple pieces simultaneously. The sliding action also provides smoother cuts through thick materials by reducing the load on the motor.
Laser guides and LED lighting systems on modern miter saws improve cutting accuracy and reduce setup time. These features help align cuts precisely, particularly important when working with expensive flooring materials where mistakes can be costly. Some advanced models include shadow line indicators that show the exact cut line without the potential alignment issues associated with laser systems.
Dust collection integration on miter saws helps maintain clean work areas and reduces airborne particles that can affect respiratory health. Many models include dust bags or ports for connecting to shop vacuum systems. Effective dust collection becomes particularly important when cutting engineered materials that produce fine particles or when working in enclosed spaces.
Jigsaw Applications in Flooring Projects
Jigsaws provide unmatched versatility for making curved cuts, intricate patterns, and detailed work in flooring installations. Their ability to make plunge cuts and follow complex cutting lines makes them essential tools for cutting around obstacles, creating custom shapes, and handling detailed trim work. The thin blade design allows for tight radius cuts that would be impossible with other saw types.
Orbital action settings on modern jigsaws allow for adjusting the cutting aggressiveness based on material type and desired cut quality. Higher orbital settings provide faster cuts through thick materials but may produce rougher cut surfaces. Lower settings or straight cutting modes produce smoother cuts suitable for visible edges or delicate materials.
Variable speed controls enable optimization of cutting speed for different flooring materials. Slower speeds work better for hard materials like ceramic tiles or dense hardwoods, while faster speeds excel with softer materials like pine or engineered products. The ability to adjust speed during cutting allows for responding to changing material conditions or cutting requirements.
Blade selection for jigsaws encompasses a wide range of tooth configurations, materials, and cutting applications. Fine-tooth blades work well for laminate and engineered materials, while aggressive tooth patterns excel with solid wood. Specialty blades designed for specific materials like ceramics or metals expand the jigsaw’s capabilities for complex flooring installations.
Dust collection and visibility features on jigsaws help maintain clean cutting lines and reduce airborne particles. Built-in dust blowers keep cutting lines clear of debris, while some models include LED lighting systems that illuminate the cutting area. These features become particularly important when making detailed cuts or working in poorly lit areas.
Table Saws for Professional Flooring Work
Table saws represent the ultimate in cutting precision and capacity for professional flooring installations. Their large cutting surfaces, powerful motors, and precision fence systems enable accurate, repeatable cuts that meet the demanding standards of commercial and high-end residential projects. The stationary design provides superior stability and control compared to portable saw options.
Rip cutting capabilities of table saws excel at reducing plank widths and creating consistent strip widths for flooring installations. The parallel fence system ensures straight, accurate cuts across the entire length of flooring planks. This capability proves particularly valuable when working with wide planks that need to be reduced in width or when creating custom width planks for specific applications.
Crosscut capabilities require the addition of miter gauges or crosscut sleds to table saws. These accessories enable accurate crosscuts and angle cuts while maintaining the precision and power advantages of the table saw. Dedicated crosscut sleds can be customized for specific flooring applications, improving both accuracy and safety during repetitive cutting operations.
Dado blade compatibility on many table saws allows for creating grooves, rabbets, and other joinery cuts necessary for some flooring installations. This capability becomes particularly valuable when working with solid hardwood flooring that requires custom fitting or when creating decorative elements like inlays or borders.
Safety features on modern table saws include blade guards, riving knives, and advanced systems like SawStop technology that can prevent serious injuries. These features become particularly important in professional settings where operators may be working long hours or cutting large quantities of materials. Proper safety equipment and procedures remain essential regardless of the safety features included with the saw.
Specialty Saws for Specific Flooring Types
Flooring saws represent specialized tools designed specifically for cutting flooring materials. These saws typically feature unique blade designs, dust collection systems, and cutting mechanisms optimized for specific flooring types. While more expensive than general-purpose saws, they often provide superior results and increased efficiency for dedicated flooring work.
Wet tile saws become essential when working with ceramic, porcelain, or natural stone flooring materials. The water cooling system prevents overheating and reduces dust while enabling clean cuts through hard, brittle materials. Diamond-impregnated blades designed for wet cutting provide long life and superior cutting performance compared to standard blades.
Vinyl plank cutters offer specialized cutting mechanisms designed specifically for luxury vinyl plank materials. These tools often use guillotine-style cutting actions that eliminate the heat buildup and potential melting associated with traditional saw blades. The result is clean, precise cuts without the burned edges that can occur with inappropriate cutting methods.
Laminate cutters provide specialized cutting mechanisms designed to handle the unique properties of laminate flooring materials. These tools often feature scoring and breaking actions that produce clean cuts without the chipping and splintering common with standard saw blades. The elimination of dust and noise makes them particularly suitable for occupied buildings or sensitive environments.
Oscillating multi-tools excel at making detailed cuts, removing damaged sections, and handling intricate work around obstacles. Their ability to make plunge cuts and work in tight spaces makes them invaluable for flooring repairs and modifications. The wide range of available blades and accessories extends their capabilities to various flooring materials and applications.
Safety Considerations and Best Practices
Personal protective equipment represents the first line of defense when operating any saw for flooring applications. Safety glasses protect eyes from flying debris, while hearing protection becomes essential when working with loud power tools for extended periods. Dust masks or respirators prevent inhalation of harmful particles, particularly important when cutting engineered materials or working in enclosed spaces.
Proper work surface setup ensures stable, secure cutting conditions that prevent accidents and improve cut quality. Sawhorses, cutting tables, and proper material support prevent binding, kickback, and other dangerous conditions. The work surface should be level, stable, and appropriately sized for the materials being cut.
Blade maintenance and replacement directly impact both safety and cutting performance. Dull blades require more force to cut, increasing the risk of kickback and other accidents. They also produce poor cut quality and may cause burning or other damage to flooring materials. Regular blade inspection and timely replacement ensure optimal performance and safety.
Electrical safety considerations become particularly important when working with corded power tools in potentially wet conditions. Ground fault circuit interrupters protect against electrical shock, while proper extension cord selection ensures adequate power delivery without overheating. Battery-powered tools eliminate some electrical safety concerns but require proper charging and storage procedures.
Material handling and cutting techniques significantly impact safety and cut quality. Proper material support prevents binding and kickback, while correct cutting techniques ensure clean, accurate cuts. Understanding grain direction, material properties, and appropriate cutting speeds helps prevent accidents and material damage.
Maintenance and Care of Flooring Saws
Regular cleaning and maintenance extend saw life and ensure optimal performance throughout demanding flooring projects. Dust and debris accumulation can interfere with moving parts, reduce cutting accuracy, and cause premature wear. Establishing regular cleaning schedules and procedures helps maintain peak performance and reliability.
Blade care encompasses proper storage, cleaning, and sharpening procedures that maintain cutting performance and extend blade life. Proper storage prevents damage to cutting teeth and reduces corrosion, while regular cleaning removes built-up pitch and debris that can affect cutting performance. Professional sharpening services can restore blade performance when replacement becomes necessary.
Motor maintenance includes proper lubrication, cooling system cleaning, and electrical connection inspection. Adequate ventilation prevents overheating during extended use, while proper lubrication reduces wear on moving parts. Regular inspection of electrical connections ensures safe operation and prevents power delivery problems.
Calibration and adjustment procedures ensure continued accuracy and performance as saws age and wear. Fence alignment, blade parallel adjustment, and cutting depth calibration should be checked regularly and adjusted as necessary. Proper calibration maintains cutting accuracy and prevents binding or other dangerous conditions.
Storage considerations protect saws from damage and environmental factors that can affect performance and reliability. Proper storage environments control temperature, humidity, and dust exposure while protecting against physical damage. Organized storage systems also improve efficiency by keeping tools and accessories readily accessible.
Cost Analysis and Budget Planning
Initial purchase costs vary dramatically between saw types and quality levels, requiring careful consideration of project requirements and long-term needs. Professional-grade saws command higher prices but offer superior performance, durability, and features that justify the investment for serious flooring work. Budget considerations should include not only the initial purchase price but also the total cost of ownership including blades, maintenance, and replacement costs.
Blade costs represent ongoing expenses that can significantly impact project budgets, particularly for large installations or when working with materials that quickly dull blades. High-quality blades typically cost more initially but provide longer service life and better cutting performance, often resulting in lower total costs. Bulk purchasing or contractor pricing can reduce blade costs for professional users.
Maintenance and repair costs should be factored into long-term ownership calculations. Professional-grade tools typically offer better serviceability and parts availability, while budget tools may require complete replacement when repairs become necessary. Warranty coverage and service network availability also influence total ownership costs.
Rental versus purchase decisions depend on project frequency, storage capabilities, and budget constraints. Rental options provide access to professional-grade tools without the high initial investment, while purchase makes sense for frequent users or those requiring specialized configurations. Rental costs can quickly exceed purchase prices for extended projects or frequent use.
Return on investment calculations help justify tool purchases for professional users. Improved efficiency, reduced waste, and superior results can offset higher tool costs through increased productivity and customer satisfaction. The ability to handle more challenging projects or work with premium materials can also justify investment in higher-quality tools.
Professional vs DIY Considerations
Skill level requirements vary significantly between saw types and cutting applications. Simple crosscuts with a miter saw require minimal experience, while complex cuts with a table saw demand extensive training and experience. Realistic assessment of skill levels helps ensure safe operation and satisfactory results while avoiding costly mistakes.
Project complexity influences tool selection and skill requirements. Simple installations with basic cuts may be suitable for DIY approaches, while complex layouts with intricate cuts may require professional expertise. Understanding project complexity helps determine whether professional installation or DIY approaches are appropriate.
Time considerations affect both tool selection and project approaches. Professional contractors require efficient tools that maximize productivity, while DIY projects may prioritize ease of use over maximum efficiency. The time value of tool learning curves and setup procedures should be factored into project planning.
Quality expectations influence both tool selection and skill requirements. Professional installations demand perfect results that may require specialized tools and extensive experience, while DIY projects may accept slightly lower quality standards. Understanding quality expectations helps guide tool selection and project approaches.
Support and training resources vary between tool types and manufacturers. Professional-grade tools often include extensive documentation, training materials, and technical support, while budget tools may offer limited resources. Access to training and support can significantly impact project success and safety.
Common Mistakes to Avoid
Blade selection errors represent one of the most common mistakes in flooring cutting applications. Using inappropriate blade types can result in poor cut quality, material damage, and safety hazards. Understanding the relationship between blade design and material properties helps prevent costly mistakes and ensures optimal cutting performance.
Cutting technique errors can compromise both safety and cut quality. Improper material support, incorrect cutting speeds, and poor body positioning can result in accidents, poor cuts, or material damage. Proper training and practice with cutting techniques help prevent common errors and improve results.
Measurement and marking mistakes can result in wasted materials and project delays. Accurate measuring tools, proper marking techniques, and double-checking measurements help prevent costly errors. The old adage “measure twice, cut once” remains relevant for flooring installations where precision is critical.
Safety shortcut temptations can lead to serious injuries and project problems. Skipping safety equipment, using damaged tools, or taking unnecessary risks may save time initially but can result in devastating consequences. Maintaining consistent safety practices protects both operators and project outcomes.
Tool maintenance neglect can result in poor performance, premature failure, and safety hazards. Regular cleaning, proper storage, and timely maintenance help ensure optimal performance and reliability. Establishing maintenance schedules and procedures prevents common problems and extends tool life.
Certified Material Testing Products (Certified MTP) is a leading supplier of construction materials testing equipment and laboratory supplies in the United States. They offer a comprehensive range of products for testing concrete, asphalt, aggregate, soil, and cement, catering to both field and laboratory applications But no matter whether they are prefered or not, the whole idea behind these tools is similar: getting a polished, shiny, and permanent effect. New to stucco or a seasoned pro, investing in good tools and learning the nuances of their use is what will get you started perfecting your craft.
Conclusion and Final Recommendations
Selecting the right saw for cutting flooring materials requires careful consideration of project requirements, material properties, and user capabilities. The investment in appropriate tools pays dividends through improved efficiency, better results, and enhanced safety. Understanding the capabilities and limitations of different saw types helps ensure optimal tool selection for specific applications.
Quality should take precedence over price when selecting saws for flooring applications. Professional-grade tools offer superior performance, durability, and features that justify higher initial costs through improved results and longer service life. The false economy of cheap tools often results in higher total costs through poor performance, frequent replacement, and compromised results.
Safety must remain the top priority throughout all cutting operations. Proper personal protective equipment, safe work practices, and well-maintained tools help prevent accidents and ensure successful project completion. No time savings or cost reductions justify compromising safety standards.
Continuous learning and skill development improve both safety and cutting performance. Understanding material properties, cutting techniques, and tool capabilities helps optimize results while preventing common mistakes. For more Any Business Card, check out this guide from NFC Business Card Investing in training and practice yields long-term benefits through improved efficiency and quality.
The flooring industry continues evolving with new materials, techniques, and tools. Staying current with industry developments helps ensure optimal tool selection and cutting approaches. Regular evaluation of tool performance and capabilities helps identify opportunities for improvement and optimization.
Future tool purchases should consider both current needs and potential future requirements. Investing in versatile, expandable tool systems provides flexibility for changing project requirements while maximizing the value of tool investments. The ability to adapt to new materials and techniques ensures continued relevance and usefulness of tool investments.